Electrolysis & Corrosion
Electrolysis
The term "electrolysis", which is a misnomer of the recreational boating community, refers to natural galvanic and accidental electrolytic corrosion. Corrosion of metals is a complex and multiform electro-chemical phenomenon: it implies electrical measurable currents and is a matter of concern for crews safety as well as money value of concerned boats.
Corrosion
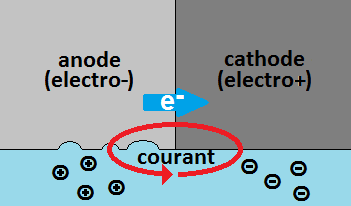
Corrosion is the result of an electrons movement (generating an electric current of opposite flow), natural or accidental, between an anode (of a given potential metal, i.e. your zinc anodes) and a cathode (less electro-negative, or, more electro-positive potential metal, i.e. your aluminium sail-drive's leg), conductively linked and immersed in the same electrolyte (i.e. sea water). There are loss of material at the anode and protection at the cathode, hence the term "cathodic protection".
Galvanic vs electrolytic
Galvanic corrosion is due to natural potential differences between different metals in contact in a same electrolyte (water), which generates a very low intensity electrical current: the corrosion current. It is effectively adressed by sacrificial anodes which deliver a protection current, opposing the corrosion current. Attention, cathodic protection such obtained must not be presumed but measured!
Electrolytic corrosion, on the other hand, is induced by an additional and accidental direct current: the stray current, which amplify in a way or another - according to polarity - the effects of the corrosion current. Attention, harmful stray currents from on board or ashore always seek going to "earth" and are responsible for accelerated corrosion of the conductive metal at the outgoing point to sea! Anodes are of no use in this case and only early detection and quick elimination will preserve your boat from costly consequences!
The corrosion potential: an essential indicator!
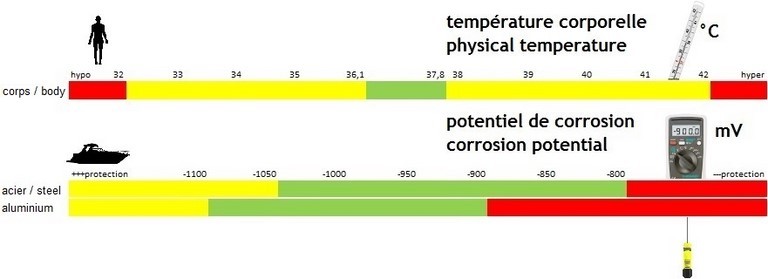
Corrosion protection of immersed metals is performed by their natural oxidation layer or by the paint system supplemented with cathodic protection (anodes...). Efficiency depends upon achieved value of their corrosion potential, expressed in (-)mV. Like human physical temperature, control is done with a dedicated device, through a simple measurement with instantaneous understanding: corrosion potential must remain within protective range (green zone above). Value shows protection level given by anodes, which are in their key role, and warns you about eventual harmful stray currents from on board or ashore.
Over and Under cathodic protection
In a same metal an anode area always destroys itself in favor of a cathode area which is thus protected. When such areas are deliberatly created by linking together different metals (sacrificial anodes) or other means, this is then called "cathodic protection".
Sacrificial anodes must always deliver the right amount of protection current to counteract the corrosion current, and be replaced when inadequate. According to polarity, stray currents may cause over- or under- cathodic protection situations.
Under cathodic protection implies more or less corrosive attacks on steel (above pic. n°2) and aluminium (above pic. n°3). It happens when corrosion potential is higher than the maximum requested value. Over cathodic protection may cause bubling and disbonding of underwater paints (above pic. n°1), if not more serious damages. It happens when corrosion potential is lower than the minimum requested value (algebraic meaning).
These may, of course, affects safety of navigation and result in costly maintenance operations or parts replacement.
Involvment of alternative AC current:mind the earthing wire!
Involvment of alternative current has not been scientifically proven concerning corrosion of immersed metal equipments of ships. However, the earthing wire of 230 V shore power might carry direct stray currents, potentially very dangerous for your immersed metal equipments if, as requested by safety regulations, it is connected to the boat's earth. This promotes indeed a corrosive loop, necessary for corrosion to occur. As you can never guess quality of shore or neighbourhood installations, prevention goes through regular control of corrosion potential and availability of appropriate protection devices: galvanic isolators or isolation transformers. It's no use tripping breakers to keep safe: the earth wire by-pass all switches...
Find out more...
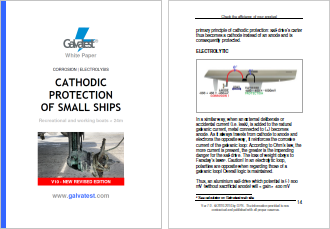
And if you are a pro...
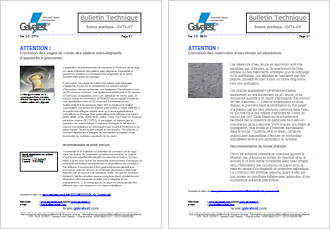
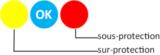
When and how to proceed?
Checking anodes during annual scrubbing off will not avoid past year damages. This is why cathodic protection control is achieved by measuring corrosion potential of an immersed metal (directly on a metal hull or in the engine room for a S-drive or propeller shaft), and verifying it remains within required protective values: (-) 1100 to (-)800 mV. Ideally, control is to be performed monthly, after each work on the boat's electricals, at winter mooring and, of course, upon suspicion. Evidence of stray currents, responsible for accelerated damages, will induce a noticeable shift of measurements during operations. To do so, Galvatest sensor is connected to a Galvatest controller or high impedance digital voltmeter, and immersed next to the controlled boat.
What do do in case of abnormal measurement?
If the measurements are outside the protection interval, your anodes are inoperative or unsuitable: it is then necessary to check their nature, their connection and their consumption. If the difference between successive measurements is significant, it is probably a harmful leakage current : disconnect the shore power and activate your circuit breakers while waiting for it to be neutralized soon. Then check by means of a new measurement that it is indeed within the protection range...
Anodes
Anodes deliver a protection current opposing the corrosion current. If it is not sufficient, then problems occurs... And regarding anodes, it is more the buyer's problem to know what he buys than the seller's one to know what he sells!
Isolator or transformer?
Galvanic isolators or isolation transformers stop stray currents from "getting" onboard through the shore earth wire. They implies different technology, reliability and effectiveness and their relative price vary from 1 to 10.
Paint blistering
In addition to over-protection, a common cause for immersed paints blistering of a steel hull, and particularly in fresh water, is the osmotic pressure difference due to indesirable soluble impurities beneath the paint layer.